The Importance of Welding WPS: Ensuring Quality and Safety in Your Projects
The Importance of Welding WPS: Ensuring Quality and Safety in Your Projects
Blog Article
Opening the Power of Welding WPS: Approaches for Performance and Safety And Security in Construction
In the realm of manufacture, Welding Treatment Specs (WPS) stand as the foundation of welding procedures, determining the essential steps for achieving both effectiveness and security in the construction process. Comprehending the ins and outs of WPS is vital to utilizing its full potential, yet many organizations battle to open truth power that exists within these files (welding WPS). By delving into the strategies that maximize welding WPS, a world of boosted performance and enhanced safety awaits those going to explore the subtleties of this crucial element of fabrication

Significance of Welding WPS
The significance of Welding Treatment Specifications (WPS) in the construction market can not be overstated. WPS serve as an essential roadmap that describes the necessary actions to ensure welds are done consistently and properly. By defining important parameters such as welding procedures, materials, joint layouts, preheat temperature levels, interpass temperatures, filler steels, and post-weld warm treatment needs, WPS offer a standard technique to welding that enhances performance, high quality, and safety and security in construction processes.
Adherence to WPS assists in achieving harmony in weld quality, lowering the possibility of issues or structural failings. This standardization likewise promotes compliance with sector policies and codes, making certain that produced frameworks meet the needed safety requirements. Moreover, WPS paperwork makes it possible for welders to replicate effective welding treatments, resulting in regular results across various projects.
In significance, the thorough development and rigorous adherence to Welding Treatment Specifications are vital for upholding the stability of bonded frameworks, safeguarding against possible hazards, and supporting the track record of manufacture companies for providing high-grade products and services.
Secret Elements of Welding WPS

Enhancing Effectiveness With WPS
When maximizing welding procedures, leveraging the key elements described in Welding Treatment Specifications (WPS) becomes vital for enhancing procedures and making my explanation the most of performance. One means to boost effectiveness with WPS is by meticulously picking the appropriate welding parameters. By sticking to the specific guidelines supplied in the WPS, welders can make sure that the welding devices is established appropriately, resulting in top notch and regular welds. Furthermore, following the pre-approved welding series outlined in the WPS can significantly reduce the time invested on each weld, inevitably boosting general performance.
Moreover, appropriate training and certification of welders in understanding and implementing WPS can better enhance performance. Ensuring that all team participants are well-versed in interpreting and carrying out the WPS accurately can lessen mistakes and revamp, conserving both time and resources. Routinely assessing and upgrading the WPS to integrate any lessons discovered or technical developments can additionally add to efficiency enhancements in welding operations. By welcoming the standards set forth in the WPS and continually seeking ways to enhance procedures, fabricators can attain higher efficiency degrees and exceptional end results.
Ensuring Security in Construction
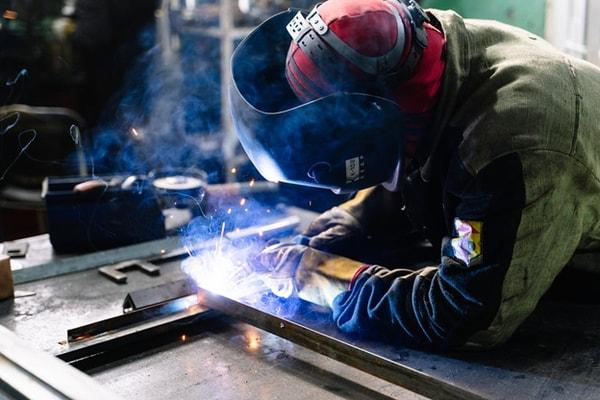
Making certain security in fabrication entails a diverse approach that encompasses numerous facets of the welding procedure. Welders should be geared up with suitable gear such as helmets, gloves, and discover here protective garments to alleviate risks connected with welding activities.
Additionally, adherence to proper air flow and fume extraction systems is essential in maintaining a healthy and balanced work setting. Welding fumes include harmful compounds that, if breathed in, can position significant health and wellness threats. Executing reliable ventilation procedures assists to minimize direct exposure to these dangerous fumes, advertising respiratory health and wellness amongst workers.
Normal equipment maintenance and examinations are also necessary for ensuring security in manufacture. Faulty equipment can bring about mishaps and injuries, underscoring the importance of prompt fixings and regular checks. By focusing on precaution and fostering a culture of understanding, manufacture centers can develop a safe and secure and efficient workplace for their employees.
Implementing WPS Best Practices
To enhance operational effectiveness and make sure top quality end results in manufacture procedures, including Welding Treatment Specification (WPS) best practices is critical - welding WPS. Executing WPS finest methods includes precise planning, adherence to market requirements, and constant tracking to ensure optimal outcomes. To start with, choosing the appropriate welding process, filler material, and preheat temperature specified in the WPS is crucial for achieving the desired weld top quality. Second of all, making sure that certified welders with the required accreditations accomplish the welding procedures according to the WPS standards is crucial for uniformity and dependability. Frequently updating and assessing WPS records to show any type of process renovations or adjustments in materials is also a vital best practice to maintain precision and importance. Furthermore, giving thorough training to welding workers on WPS demands and best practices fosters a society of safety and top quality within the construction environment. By faithfully carrying out WPS best techniques, producers can streamline their operations, minimize mistakes, and provide exceptional items to meet customer expectations.
Final Thought
To conclude, welding WPS plays a vital duty in guaranteeing performance and safety in fabrication procedures. By concentrating on key aspects, improving performance, and executing ideal practices, business can maximize their welding operations. It is important to focus on precaution to stop crashes and ensure a smooth production process. By complying with these methods, organizations can open the full potential of welding WPS in their construction operations.
In the world of fabrication, Welding Procedure Specifications (WPS) Go Here stand as the foundation of welding operations, dictating the needed steps for accomplishing both effectiveness and security in the fabrication process. By defining essential parameters such as welding procedures, products, joint layouts, preheat temperature levels, interpass temperature levels, filler metals, and post-weld heat treatment needs, WPS give a standard technique to welding that improves effectiveness, quality, and safety in construction procedures.
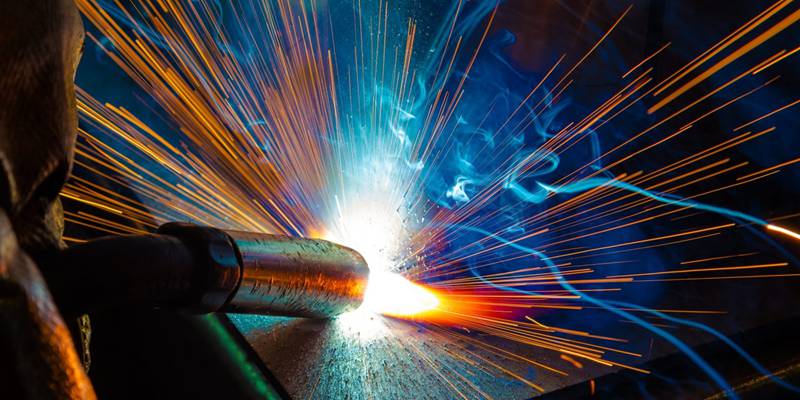
When optimizing welding procedures, leveraging the key elements outlined in Welding Treatment Requirements (WPS) ends up being vital for maximizing and enhancing procedures efficiency. (welding WPS)
Report this page